Demonstrated Torrefaction Technology to License
HM3 Energy’s demonstrated torrefaction technology is available to license. Its patented HM3BiocoalTM technology was perfected over a three-year period in a demonstration plant using a commercially scaled torrefier and densifier.
Commercial Equipment – The torrefier (1.5 tons/hour) and densifier (5 tons/hour) were commercial in scale. All other equipment was commercial in design.
Numerous Test Runs – Multi-day production test runs with continuously operating, linked equipment were conducted. A variety of feedstocks, including juniper and pine forest residue, mill residue and agricultural residue, were made into sturdy, water-resistant biocoal.
Successful Testburns – HM3BiocoalTM was successfully testburned in Western Research Institute’s coal boiler in 2017. Not only did it grind easily prior to feeding to the boiler, the combustion sustained throughout the test was comparable to western (sub-bituminous) coal.
Innovative Torrefaction Technology
HM3’s streamlined torrefaction and densification technologies are the result of 10 years of careful research and development.
Simple Torrefier Design – HM3’s patented mass flow torrefaction system is inexpensive to build and easy to maintain, with few moving parts. Using gravity, feedstock evenly torrefies as it flows down the reactor.
Densification – HM3 Energy’s densification system uses a densifier modified with our patented die cooling system and a unique post-densification conditioning process. Together, they produce sturdy, water-resistant HM3BiocoalTM without need to add binders.
Cheapest Feedstock – HM3’s torrefaction process easily uses forest waste to consistently produce high quality HM3BiocoalTM; other torrefaction processes mostly require more expensive clean wood chips as feedstock.
HM3 Energy recently completed its work on a US Forest Service 2019 Wood Innovation Grant Award. Wood Innovations Grants support development of products that use excess forest material. HM3’s grant work established that HM3BiocoalTM produced from forest waste competes in price with white pellets for export to Asia as coal replacement fuel.
Senior Technical Team Members
HM3 Energy’s technical team members have all worked in multi-national corporations and have deep knowledge and experience in product/process development, chemical plant construction and operations, wood biomass chemistry and business management.
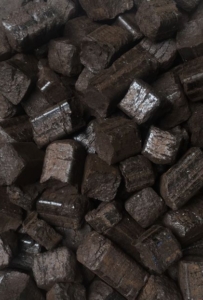
“High costs have been a major stumbling block to advancing a robust commercial production of biocoal. HM3 Energy has taken the time to address all factors impacting cost — feedstock costs, simplicity of design, maintenance costs, energy efficiency and a process that doesn’t use any binders at all — to create a true waste-to-energy biocoal technology that easily competes with white pellets at the coal plant burner tip, making it the torrefaction technology to license. ”
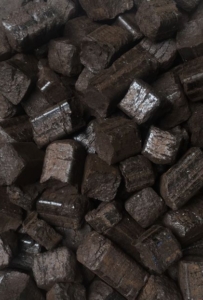
Biocoal: 2nd Generation Biomass Energy
With recent technological advances, biocoal and black pellets are poised to become the biomass energy of choice. HM3 Energy is making its torrefaction technology available to license.